I finished setting up the new bandsaw mealier this week, so last night i got back to the wine rack. The only thing worth reporting, is how I sand small parts like those in the rack. When it comes to small parts, the only method I’ve found to give acceptable results, is “lapping”. Forget your power sanders, they will just round over the edges, even sanding blocks can be problematic, depending on the size of the parts. Next time you need to sand some small parts, find a flat surface and tape down some sand paper, you won’t regret it.
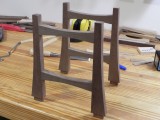
Coming together nicely.
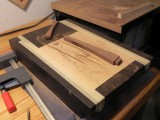
Sanding small parts
My wine rack project is on a little hiatus, while I set up the newest addition to my shop, a Rikon 14″ deluxe bandsaw. I have lived without a bandsaw for years, because all my projects where strait and kind of bland. The few times I’ve needed to make curved parts, I made do with router templates and my jig saw. Lately I’ve been making more curvy pieces, and it’s become obvious that a bandsaw is a necessity. after a few weeks of researching, I settled on the Rikon, because it meet my free primary requirements. It costs less than $1k, it runs on 120 volts, and it has an excellent re-saw capacity of 13 inches. Hopefully I will have it all tuned up, and ready to go by the end of the weekend.
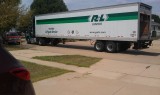
I'm sure the neighbors loved me for this.

A metal pallet?
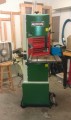
4 hours of assembly later.
It’s time to make some tenons and try out my new flush trim bit. I’ve go On of the big purpose built table saw accessories for making tenons, but I’ve found that my crosscut sled a ripping blade and scrap wood does a better job. All you need to do is clap or tape some crap wood to the base and back of the sled. This provides a perfect “zero clearance” surface that will prevent chip-out. Then all you need to do is set the blade height and go to town.
I’ve been looking forward to the pattern routing part of this project, since it started. I’ve been excited about taking my work to the next level, but also a little nervous, because I didn’t start small. Every singe board in this project has at least one curve on it. Aa the old saying goes, “go big or go home”. It turns out I didn’t need to be nervous, because the compression bit left a surface that will only require light sanding, plus one for modern technology.
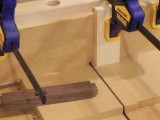
chip out free tenoning jig

ready to rock and route
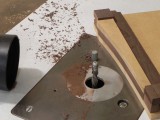
One down many to go
I spent very little time in the shop over the last week, because it was the hurry up and wait time of the project. Since my shop is a garage with no real climate control, I have to take my time milling up lumber. My routine is strait forward, and starts by flattening a face, and then letting the boards rest for 24 hours. The next step is to thickness plane the boards, I don’t take them down to final thickness, just down enough to make them uniform across the entire board. I then let the boards rest for 24 hours. I then repeat this the process on the edges. I run through the entire process one more time to bring the boards to finished thickness & width before I start cutting joinery. It takes a long time, but it guarantees my boards stay strait and true.
Since I spent most of the week doing nothing, I was itching to get into the shop over the weekend and start doing something. As I stated in an earlier post, this is my first project I’ve made that used mortise and tenon joinery, so I took my time and set up the router table to rout out the waste. One thing I have to admit, is buying the spiral up bits was one of the best purchases I’ve ever made. Once I got the waste removed i set to work squaring up the ends using my chisels. I think for a first attempt, I did pretty well. The following photo is inspired by Chris schwarz, and all the black & white photos he posts on his blog.
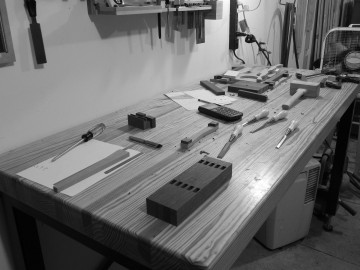
So what can you do when you spend 16 hours over two days in the shop? Well you can do several things, one is rough mill some stock to width, second you can drink more Gatorade than you thought humanly possible, and three you can make a really unimpressive MDF template. How impressive it is, probably depends on who you ask. The general public would probably say it’s just a board with some curves on it. I’d like to think that a skilled woodworker can look at it see how much work went into making it. This little template required two jigs to produce, and it’s only 90% done. In my opinion that’s an awful lot of work, for something that won’t even end up in the finish piece, but that’s the price of taking your work to the next level.
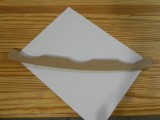
16 hrs worth of work to produce......
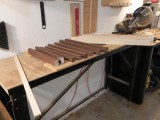
rough milling phase one