I was on vacation last week so I built myself a collapsible spray booth. The walls are made up of 8: 45″ by 90″ panels. The corners are formed by joining 2 panels with door hinges; thus allowing the booth to be collapsible for storage. The 4 corner units are bolted together using 2 parallel boards: 1 along the top of the wall, and 1 along the bottom. The top of the booth is a single sheet of plastic film held in place by the top parallel boards.
Continue Reading…
I was cutting some aluminum to size lat night for my chip shield project, and was amazed at the surface finish I achieved.
The details:
- 7075-T6 1.5″ x 2.5″
- Jet 5×6 horizontal bandsaw
- 10-14 TPI variable pitch bi-metal blade
- 120 SFPM
- no cutting fluid
612×816 456kB
1224×1632 1217kB
Last week, I Used some gift cards I got for Christmas to pick up a Delmhorst J-Lite moisture meter. It’s a lower end model that requires you to manually correct the readings for temperature and species. Unfortunately the charts provided by Delmhorst are a little course.
Fortunately the data contained in the charts is fairly well behaved, and thus easily curve fitted. After an hour or two of data entry and curve fitting I cam up with an excel spreadsheet. The spreadsheet takes the following 3 Inputs.
- Temperature in °F
- The J-Lite Meter Reading (drop down list)
- The wood species being tested (drop down list)
The spreadsheet takes the inputs, and does some vlookups to determine what the corrected moisture content is. The spreadsheet can be downloaded here.
It’s been a while since I posted something so I thought I should share what I’m currently working on. Besides, it’s to cold in the garage to work even with the propane heater running full blast. I’m Making 2 utility benches for my workshop. I want them to last “forever”, so I have over engineered everything. My design requirements where:
- They must be open underneath for role away tool storage.
- They must be easy to disassemble if/when I move.
- They must be able to support a high static load, in case I want to mount machine tools to them. I chose 1000 pounds as the target load.
It took me awhile to finalize the design, but what I came up with should be easy to build and not cost to much. The overall dimensions are W 72”, D 30”, H 40”– 44” (adjustable). I plan to make the top 4″ thick out of laminated hard maple. I might make it thinner depending on how much maple costs per board foot when I go to purchase it. The legs & horizontal cross bracings are 2.5” x .12” square tubing, & the rear diagonal bracing is 1-1/2” x 3/16” flat bar bolted to the legs.
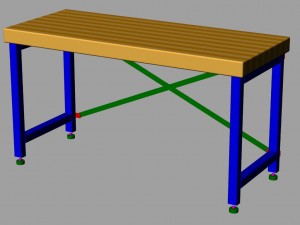
I’ll post some more pics in a day or two.
I have purchased several sanding blocks over the years, and I’ve never found one that I really liked. I had some extra maple laying around the shop, so I turned it into 2 sanding blocks. They are 6-1/2″ long & 2-3/8″ wide. The top and bottom halves are held together with a 1/4″-20 bolt, and a custom knurled nut. The most time consuming step was using the belt sander, to give the tops a gentle arch. The following are some pics of the model & a finished block.
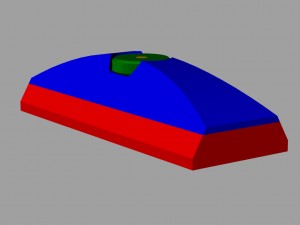
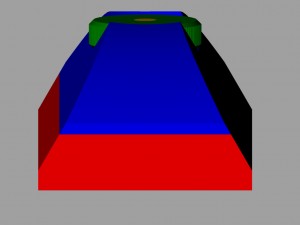
Continue Reading…